3.5 Challenges in modern aerostructures
3.5.1 Sandwich structures and composite materials
- High stiffness with low weight material configuration
- Core carries the shear load which the face sheets carry the tensile and compressive loads associated with bending
- Early example of sandwich structure was De Havilland Mosquito which had balsa core sandwiched between spruce face sheets
- Carbon and boron fibers are commonly used face sheets due to high specific stiffness and specific strength
- Core is often constructed of foam with high compressive strength
- Core and face can be adhesively bonded or molded in place
- Other cores are corrugated metals or metallic foams
- Early composite aircraft was the Raytheon/Beach Starship 2000 (1986)
Metalic foams permit shear loads to be carried by a low density (porous) structure.
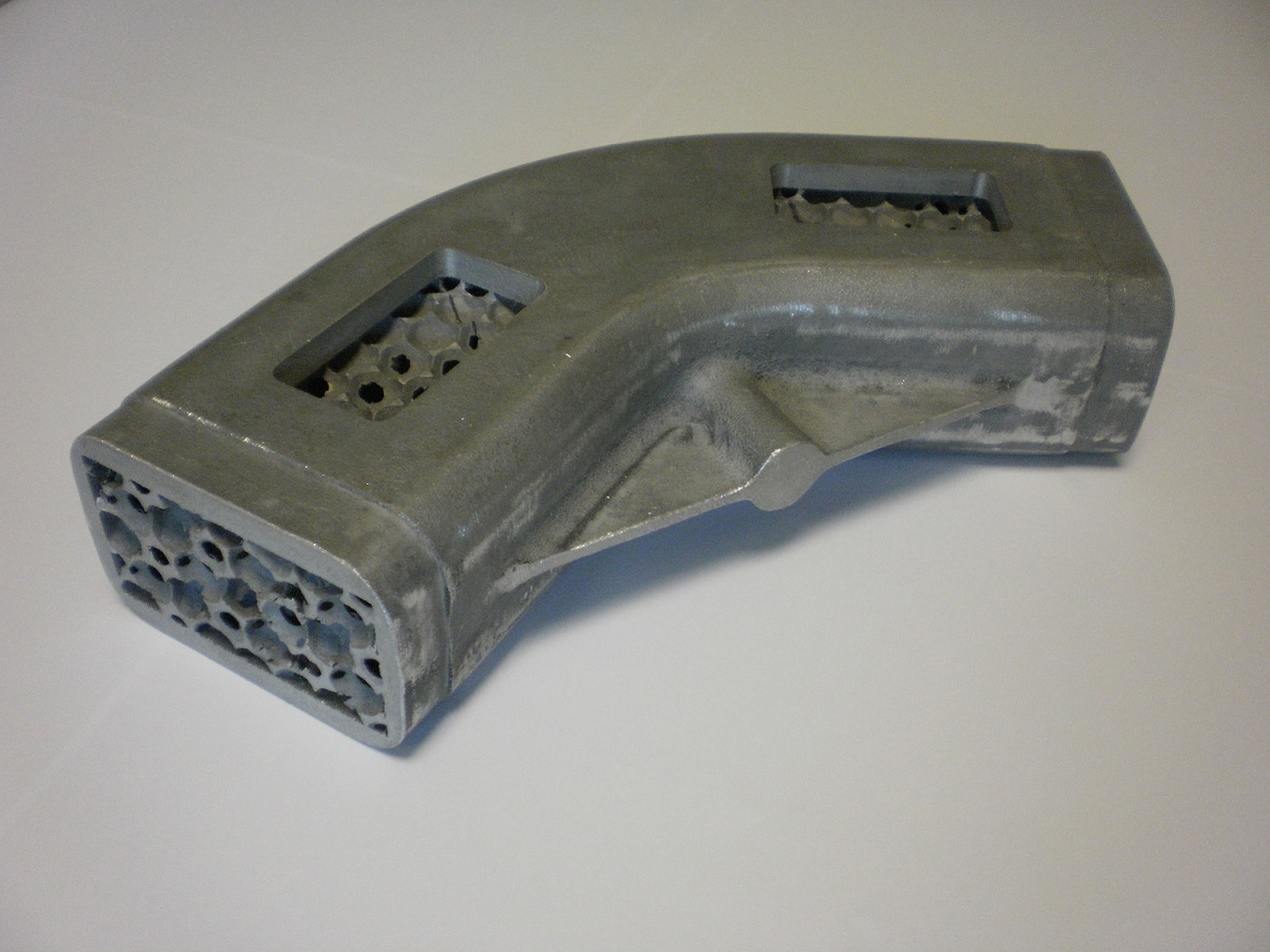
Blanchet matthieu, CCSA3.0, 2012
It also may serve multiple functions, ie, cooling
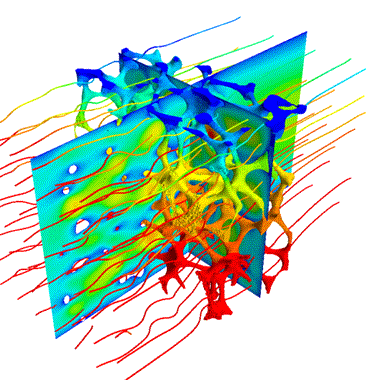
Jean-Michel Hugo, CCSA3.0, 2012
3.5.2 Tailored stiffness–composite materials
- Aeroelastic tailoring: use of directional differences in properties to carry load and cause intentional deformations that have aeroelastic advantages (stiffer in one mode of deformation than another)
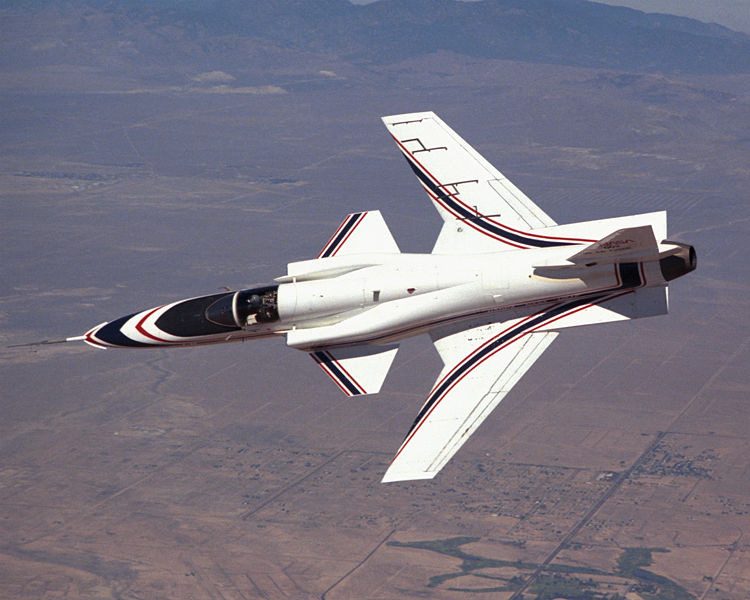
NASA
- Grumman X-29A–Forward swept wing with aeroelastic tailoring.
- The advantage is that the wing tips stall last instead of first, allowing greater control
- Downside is that the aeroelastic deformation causes positive feedback on wing loading (wing loading drives higher angles of attack, drives higher wing loading)–Divergence
- Bend/twist coupling allows minimization of divergence effects
3.5.3 Wing warping
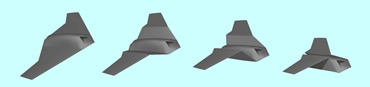
@TAMU2014
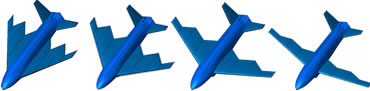
@TAMU2014
Challenges
- Maintain structural integrity during large changes in configuration
- Control